On a recent sunny Friday, Richard Laliberte stepped through the back door of Best Buy Canada’s former headquarters.
Inside, Geek Squad chatter is now replaced with the hum of a modern assembly line. Robotic arms spin through the air, cutting and stacking components at rapid speeds.
Squint hard enough and you might think you’re in the presence of a high-tech printing press. Step closer and a roll-to-roll lithium battery production line comes into focus. Burnaby-based Svante Inc. has adapted the machinery to produce a carbon-sucking laminate the company says it hopes will transform humanity’s fight against climate change.
“It never stops.” said Laliberte, Svante’s chief operating officer. “We need to show the world we’re ready to commercialize.”
When the machines go into production next month, Svante’s new factory will become the first plant in the world to commercially produce filters that can snatch carbon out of a smokestack or even thin air.
For now, the facility is powered by roaring shipping-container-sized generators as it awaits a massive electrical upgrade from BC Hydro. At full capacity, Svante claims the production line will be able to manufacture enough filters to remove 10 million tonnes of carbon a year — equivalent to the emissions from 27 million cars.
B.C. factory first to commercially produce filters for carbon capture
Svante’s sprawling 141,000-square-foot facility is filled with laboratories that specialize in quality control, machine engineering or the development of a new material that could underpin the next generation of carbon capture technology.
Some are fitted with high-powered microscopes to analyze how the filters handle thousands of hours of use. Others test performance at different humidity levels, from the dry desert to the sticky tropics.
The largest device in the building by far is a 14-metre-wide carbon capture machine, nicknamed “The Buck.” Standing as a demonstration to potential customers, the spinning machine is capable of capturing 500 tonnes of carbon dioxide (CO2) per day. Another bigger machine stored off-site captures four times more.
Once installed, Svante’s carbon capture process is continuous. Polluted flue gas is forced through one of 48 filter modules at a time, with the nanomaterial inside trapping carbon molecules like flypaper. Once saturated, the filters rotate to a cooling stage before getting blasted with steam to release the captured CO2 for storage or reuse.
BIV was shown the technology on condition it does not reveal details that Svante said it fears could be stolen by competitors.
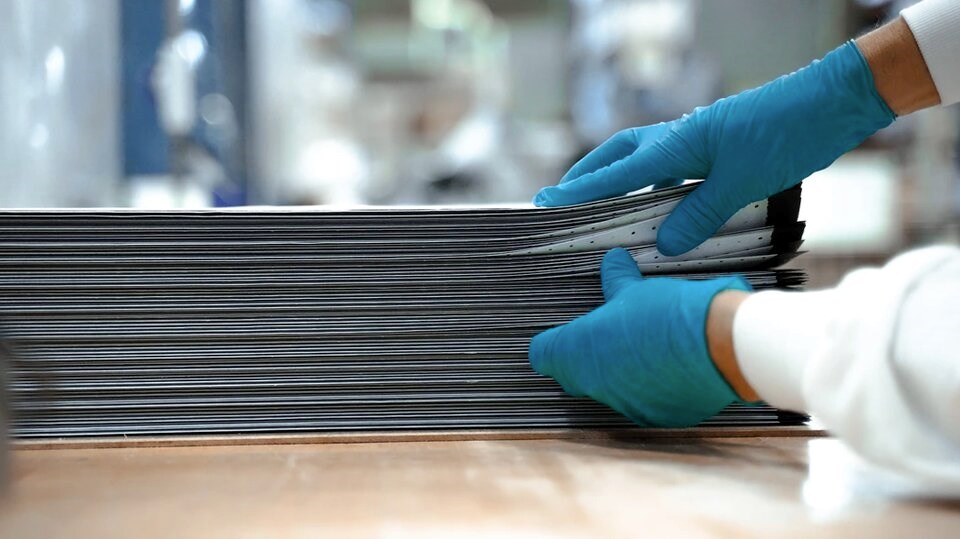
Capture technology works but cost varies
There’s a lot at stake. To date, the company has raised roughly US$600 million and employs close to 350 employees — a combination of engineers, scientists and blue-collar assembly workers.
Named after Svante Arrhenius — a Swedish scientist who played a key role in the emergence of modern climate science — the company this year ranked 38th on Time Magazine’s list of the world’s Top 250 clean tech companies.
So far, the company’s success has been built on its novel nanomaterial that gets applied to laminate sheets as paste and stacked into filters capable of capturing up to 95 per cent of CO2 from industrial flue gas, said CEO Claude Letourneau.
“We’ve cracked the code of technology. That’s done,” Letourneau said. “We now need to crack the code of monetization.”
Companies around the world are racing to engineer carbon capture machines that can either pull CO2 out of an industrial smokestack or directly out of the air.
The industrial version — described by Svante as point-source carbon capture — tends to cost less than $250 per tonne. But drawing carbon through direct-air capture from the atmosphere, which has much lower CO2 concentrations, can double or even triple costs.
Government rebates key to carbon capture's early growth
The debate over carbon capture and storage has become a central battleground in Canada’s climate policy landscape. Critics view it as a costly distraction — a lifeline that ultimately delays a necessary shift away from fossil fuels and potentially enables further extraction.
But for proponents such as Letourneau, the technology is a crucial tool to decarbonize heavy industry and transition to a lower-carbon future.
A chemical engineer, Letourneau was part of early attempts to manufacture electric vehicle batteries in the 1990s. He has also worked for what was then SNC-Lavalin building aluminum smelters around the world.
Now 65, Letourneau said he got into the carbon capture industry as governments and private companies were looking to invest in engineered climate solutions.
Letourneau pointed to the U.S. government’s $85-per-tonne tax rebate given to companies who pursue the technology.
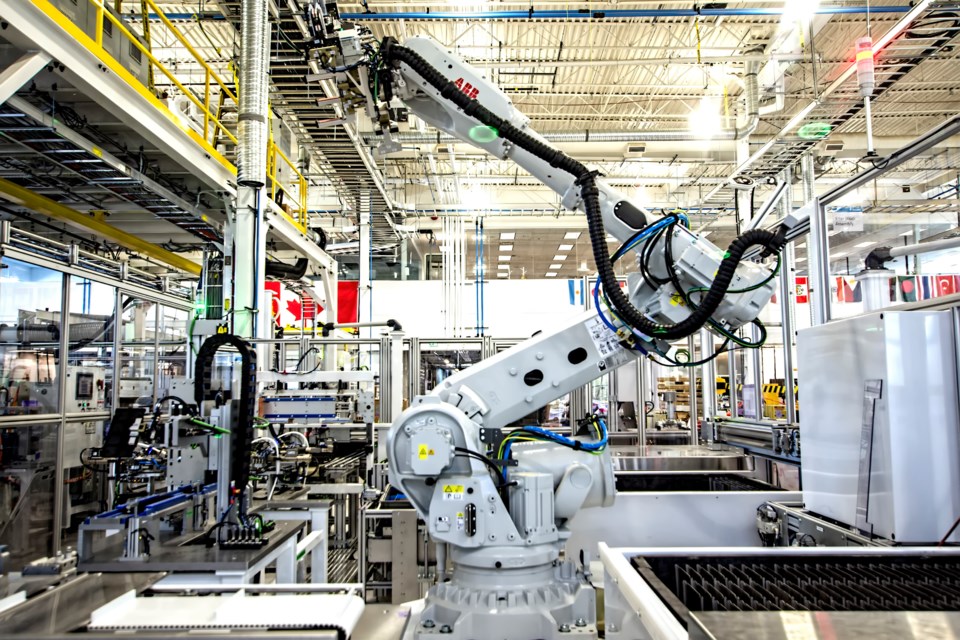
Canada’s system is even more generous, providing investment tax credits to cover up to 62 per cent of capital costs for a carbon capture project.
On top of that, the country’s industrial carbon pricing system provides credits to companies that reduce their emissions below a specific threshold. The credits can be sold to high emitters, creating an additional revenue stream once carbon capture projects are operational.
The idea is to convince big polluters to stop polluting so much today, so that society pays less in the future.
“At the end of the day, we need to have worldwide industrial policies that say, this is the price we put on carbon, and you guys have to either do it and not emit or pay that extra price,” Letourneau said.
Government policy, private investment key to emerging capture industry, says CEO
Questions around the role of carbon capture technology have taken on added urgency as Canadians prepare to vote in their next federal government. The two leading contenders — Liberal leader Mark Carney and Conservative leader Pierre Poilievre — have said they would support the technology in different ways.
While Carney continues to back the industrial price on carbon, if elected, Poilievre said he would axe the program and roll out a tax credit that Letourneau says appears like that of the U.S. system.
But it’s not clear where that money would come from or how companies would choose to spend it. Without an industrial price on carbon, Svante’s CEO said he believes the economic incentive for companies like his would vanish.
“No project will be done here in Canada,” Letourneau said. “That’s it. Finished.”
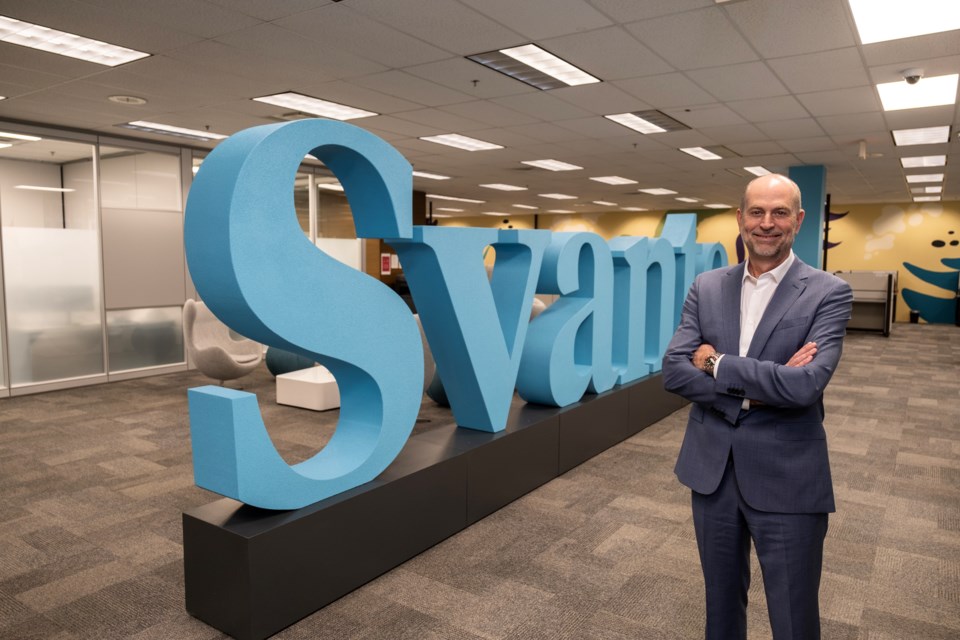
Beyond government, big companies like Microsoft, Shopify and JP Morgan have increasingly backed carbon capture projects with the stated aim of offsetting their own emissions through the voluntary carbon market.
In many ways, B.C. has become a hot spot for the technology. Carbon Engineering developed a pioneering direct-air capture plant in Ƶappbefore selling it off in 2023 to a subsidiary of the U.S. oil and gas company Occidental Petroleum. The US$1.1 billion deal came as the fossil fuel company looked to build the largest direct air capture project in the world in Ector County, Texas.
Earlier this month, Microsoft signed a deal with Vancouver-based CO280 Solutions Inc. to develop carbon capture projects at several U.S. pulp and paper mills.
CO280 said the projects will remove about 3.7 million tonnes of CO2 over 12 years, but declined to reveal the value of the deal or where the machines would be installed.
Between private investments, government tax credits and an emerging carbon market, Letourneau said carbon capture companies are starting to see a chance at profit.
“Now, you’re looking at a very nice revenue stream,” he said.
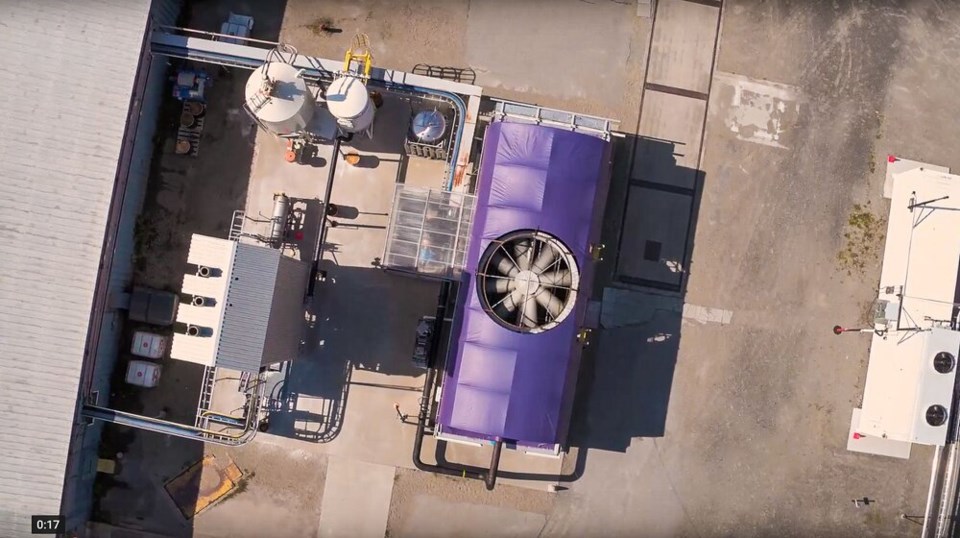
A costly gamble or an essential stop-gap?
There’s a story staff at Svante like to tell. Picture an overflowing bathtub representing Earth’s beleaguered climate system. The running tap? Humanity’s relentless gush of greenhouse gas emissions from burning fossil fuels.
For company spokesperson Colleen Nitta, the analogy is a powerful one. The immediate response to a flooded bathroom isn’t to debate the tap’s flow rate, she argues, but to intercept the water before it hits the already-full tub.
In this watery scenario, the technology snatching CO2 from industrial smokestacks before it enters the atmosphere is akin to placing a bucket under the faucet. Direct-air capture, the nascent field of sucking CO2 directly from the air, is like trying to mop the bathroom floor, or perhaps lower the water level with a soup spoon.
But for critics of carbon capture, its potential as a “bucket” to staunch the flow of oil and gas emissions looks more like a gilded thimble — an expensive and inefficient approach that ultimately fails to address the core problem of the still-gushing tap of fossil fuel extraction and combustion. Their argument: Wouldn’t it be far more effective, and economical, to simply dial back the flow until it’s little more than a drip?
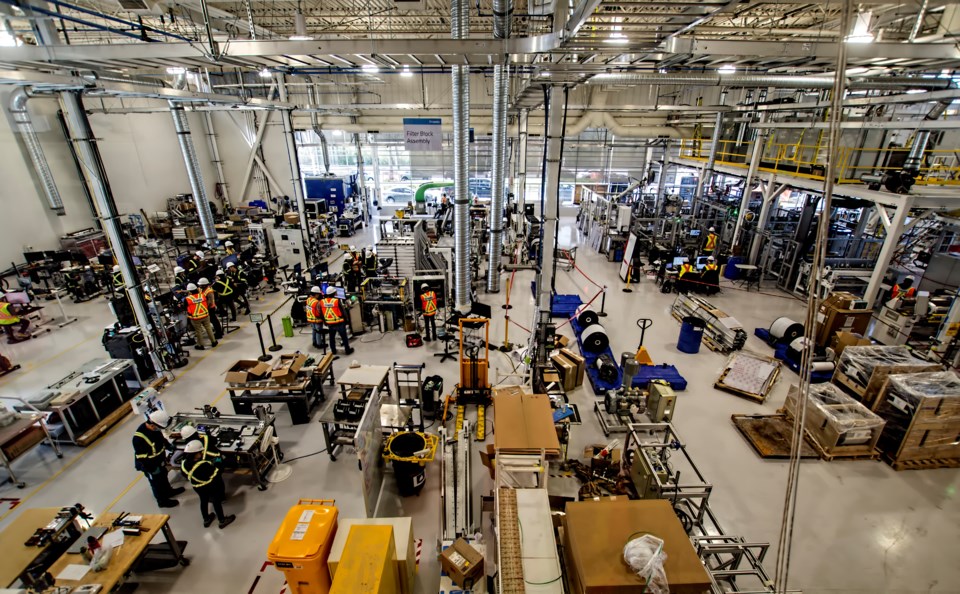
In January, an analysis looking into two existing carbon capture projects in Alberta found the cost to capture one tonne of emissions exceeded the maximum federal carbon price of $170 per tonne. That figure is a key indicator of the future viability of carbon capture revenue streams.
Mark Kalegha, an energy finance analyst who carried out the study for the Institute for Energy Economics and Financial Analysis (IEEFA), concluded that public funding of the Pathways Alliance carbon capture projects was “misguided” and represented a “costly gamble that may not yield tangible results.”
“The projects are economically challenged,” Kalegha told BIV. “Commercial-scale projects in Alberta are reporting rising operating costs with relatively flat revenue.”
One of Canada’s largest tests of carbon capture technology was built at the SaskPower Boundary Dam 3 coal plant at a cost of $1 billion.
After nine years of operation, the plant captured 57 per cent of its carbon emissions and never hit the annual 90 per cent capture target, according to the IEEFA. Carbon captured for the project was later used for enhanced oil recovery, likely leading to an increase in overall emissions, the report found.
Some experts see limited role for carbon capture
Chris Bataille, an adjunct professor at Simon Fraser University and a research fellow at the Columbia University Center on Global Energy Policy, said carbon capture works at a thermodynamic and engineering level but remains “incredibly expensive.”
“It’s really not coming on all that fast at all,” Bataille said. “It really has to be seen as a backup.”
Bataille spoke to BIV from Norway after visiting the first cement plant in the world to deploy a commercial-scale carbon capture machine. He said he is supportive of the capture technology, especially in hard-to-decarbonize industries that humanity still needs, such as cement, pulp and paper, fertilizer and aviation.
Outside of those areas, Bataille said it would be more efficient to pursue other lower-cost emission-reduction strategies such as electrification and controlling fugitive methane emissions. Still, he acknowledged, there will be remnant emissions.
“Carbon capture and storage is about building our goalie,” Bataille said. “But I wouldn’t be making half-century bets on carbon capture and storage for the oil sands.”
Bataille said there are some reasonable applications of the technology in the fossil fuel industry, such as lightening bitumen so it can flow down pipelines.
But he said industry is still struggling to put carbon capture technology on the back of a steam-assisted gravity drainage, or SAG-D, plant — an extraction technique popular in Alberta’s oil sands that releases vast quantities of greenhouse gases.
“The simple fact is, you can’t have just tech,” said Bataille. “And until there’s strong policy to adopt the tech, the tech is never going to develop.”
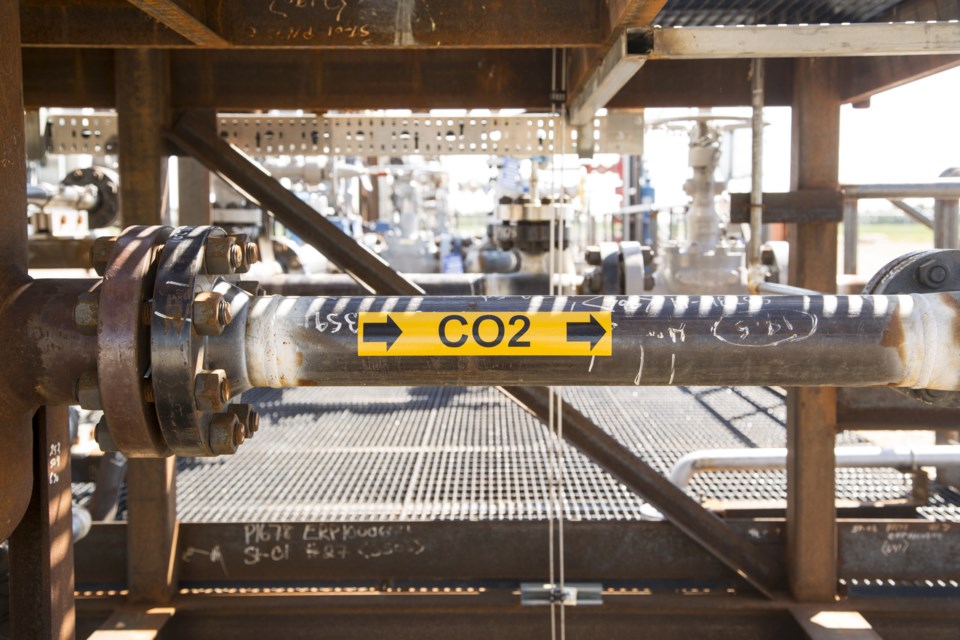
Erik Haites, an economist with Margaree Consultants Inc. and an author of multiple United Nations climate change reports, echoed that sentiment.
“Many, many, many reduction options are cheaper than carbon capture and storage today,” he said, pointing to the European Union’s industrial carbon price, which is driving down emissions at a cost of less than 100 euros per tonne.
Haites said he is also wary of big tech companies looking at carbon capture to hit their emission-reduction targets and look good in front of customers and investors.
“That’s part of their public relations exercise,” Haites said.
Emily Eaton, a researcher at the University of Regina studying the carbon capture movement, points to what she says is an even more fundamental flaw.
Applied to the oil and gas sector, she said carbon capture only targets emissions released during the extraction and processing of fossil fuels — a relatively small fraction, accounting for just 10 per cent of the sector’s total greenhouse gas footprint. The remaining 90 per cent is unleashed when those fuels are ultimately burned.
“We know that over 80 per cent of the world’s greenhouse gas emissions come from fossil fuel,” Eaton said. “So then the question is, does carbon capture help us phase out the production and use of oil and gas?
“And I think the answers there so far have been no.”
Carbon capture opponents driven by 'pure ideology,' says CEO
Letourneau sees the world’s energy future through a different lens. He said the expectation of living in a world without oil or gas is not realistic, at least for now.
Calls to halt carbon capture projects on fossil fuel infrastructure will only miss a chance to avoid pumping more carbon into the atmosphere, added the CEO.
“This is pure ideology, and this goes nowhere,” Letourneau said.
Despite the skeptics, Svante is forging ahead. Its board and management retain control of the company’s direction despite millions of dollars of outside investment.
And while no one investor owns more than 15 per cent of the company, its current ownership structure — with 40 per cent held by oil and gas companies, 40 per cent by private investors and the remainder by management and strategic partners such as United Airlines and General Electric — underscores the complex web of interests surrounding carbon capture and storage.
Svante’s early backers were from oil and gas, with Husky (now Cenovus), Chevron and the Oil and Gas Climate Initiative — a fund established by 12 of the world’s largest fossil fuel companies — all providing crucial early investments.
That money helped Svante fine-tune its technology at demonstration projects inside fossil fuel facilities in Saskatchewan and California, as well as at a Lafarge cement plant in Richmond.
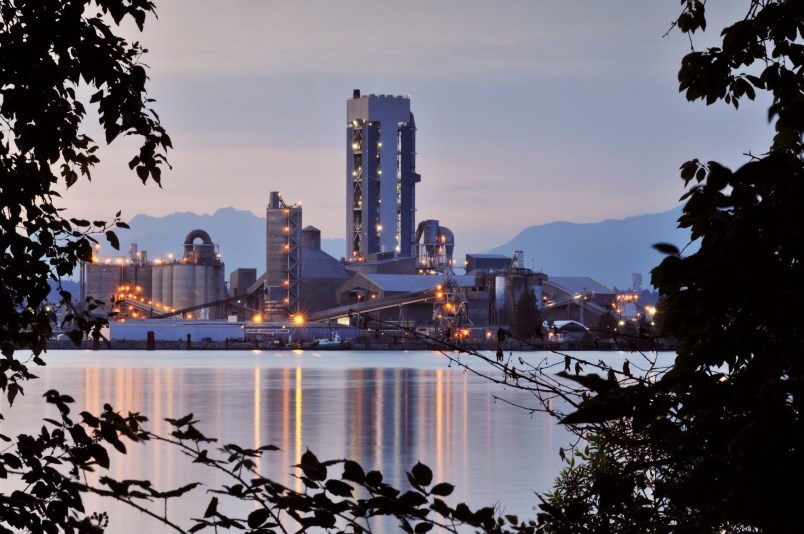
More recently, Svante signed an agreement with a venture capital arm of 3M to ramp up production of filter input materials as demand picks up. And in January, the company struck a memorandum of understanding with the Nebraska-headquartered company Tenaska to help transport and inject carbon deep underground where it can be stored in saltwater reservoirs.
Svante plans to direct early sales of its filters and machines at pulp and paper mills, ethanol plants and waste-to-energy facilities.
After that, the company is eyeing commercial expansion into cement and steel plants, and the fossil fuel sector — all while supplying filters to large players in the direct-air capture business.
Letourneau’s ultimate goal is ambitious: To capture 30 per cent of the global market for carbon capture filters so he can supply 100 plants a year for the next 30 years.
The path forward for carbon capture remains uncertain. Companies like Svante are making technological strides and benefiting from government incentives. But fundamental questions persist around cost-effectiveness, scalability and its role in either enabling or hindering the transition away from fossil fuels.
Now weeks away from becoming a key supplier for the nascent industry, Svante is setting itself up to help answer those questions — one way or another.